Case Study
Digitizing Field Reporting on the Prairies with Buffalo Inspection Services
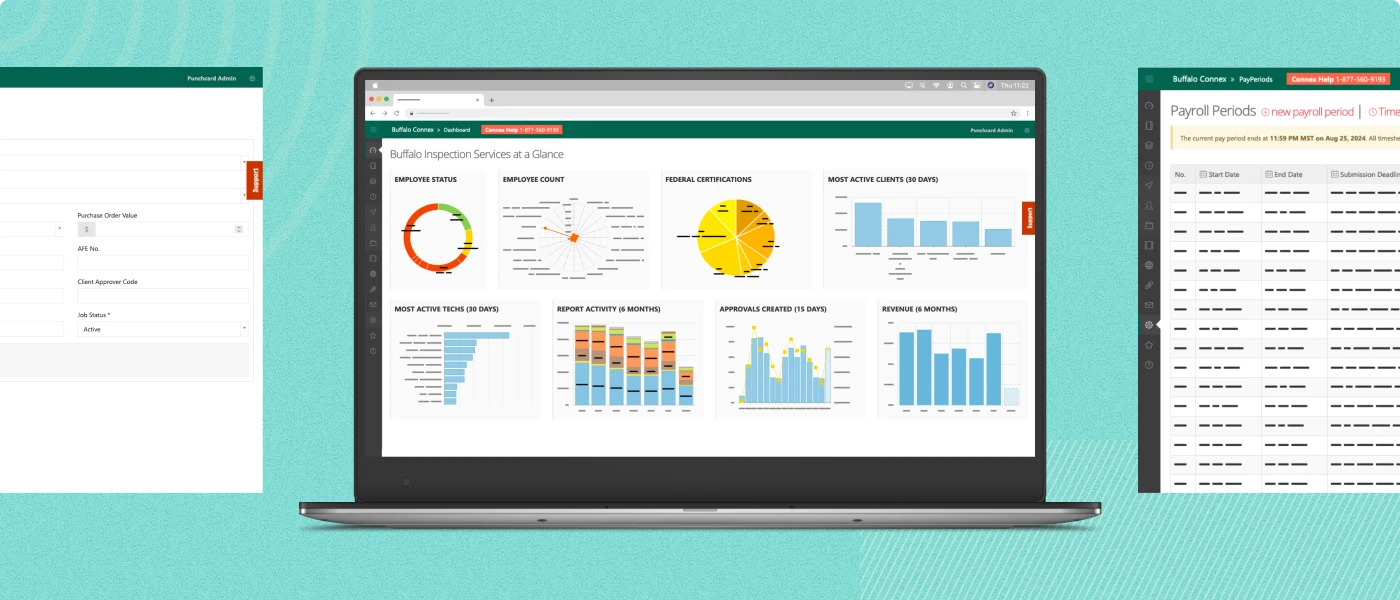
Client

Services
Custom Development
Platforms
Web Application

The Problem
Imagine you’re a field technician conducting inspections on the integrity of oil & gas pipelines in a ditch on the side of the road in the middle of the night out in the middle nowhere.
You’re isolated, alone, and surrounded by an infinite expanse of pitch-black sky and the deafening sounds of silence buzzing in your ear. Your only beacon of guidance is the dim light escaping from your work truck that you use to hastily fill out your inspection report that’s due to head office in just a few short hours.
As you might think, these paper-based reports completed in the dead of night by camper van light lack consistency, standardization, and are riddled with manual data entry errors. Often these reports would be lost amongst a slew of other paperwork including work orders and invoices that would line the dashboards of many independent contractors’ trucks.
In fact, on more than one occasion, missing invoices were tragically found months overdue, stuffed underneath the seats of vehicles—with no hope of ever being collected on—the eventual catalyst for digital transformation at Buffalo Inspection Services.



The Overview
Recognizing strict regulatory compliance & federally mandated requirements of non-destructive testing (NDT) reporting and plagued by inefficiencies in their current paper-based data entry process, Buffalo Inspection Services understood just how liable and vulnerable their business operations were to incorrect documentation and data entry errors.
At the end of the day, a minor error in reporting could be the difference between Buffalo remaining in business or not. As a result, they sought a digital solution to help reduce inefficiencies and de-risk their business operations.
Initially, Buffalo engaged with Sam Jenkins and Estyn Edwards, who would eventually form the basis for Punchcard Systems, to help build a simple integration with QuickBooks, but by 2013 the duo had completely revolutionized Buffalo’s manual, paper-based process with a digital reporting and data entry system that transformed the way they did and continue to do business today.
Inadvertently becoming Punchcard’s very first client in the process, Buffalo would now be able to digitize their reporting process—establishing quality assurance and quality control measures to preserve the highest levels of data quality and data integrity in their reporting system.
In early 2013, Buffalo Connex launched as a portal designed to streamline data entry and digitize the field reporting process. The custom job management platform allowed service technicians and contractors to input their test results remotely from the field directly into a digital system—providing a centralized location to manage and track work orders, inventory, project hours, equipment, and invoicing.
Impact by the Numbers

“The Buffalo Connex portal is simple and user-friendly. New technicians to Buffalo always comment on how it is the best system they have ever used.”
Ross Hutchison
President
5+ Million
examinations performed
231,000+
work orders
568,000+
individual reports filed
20+
inspection methods supported
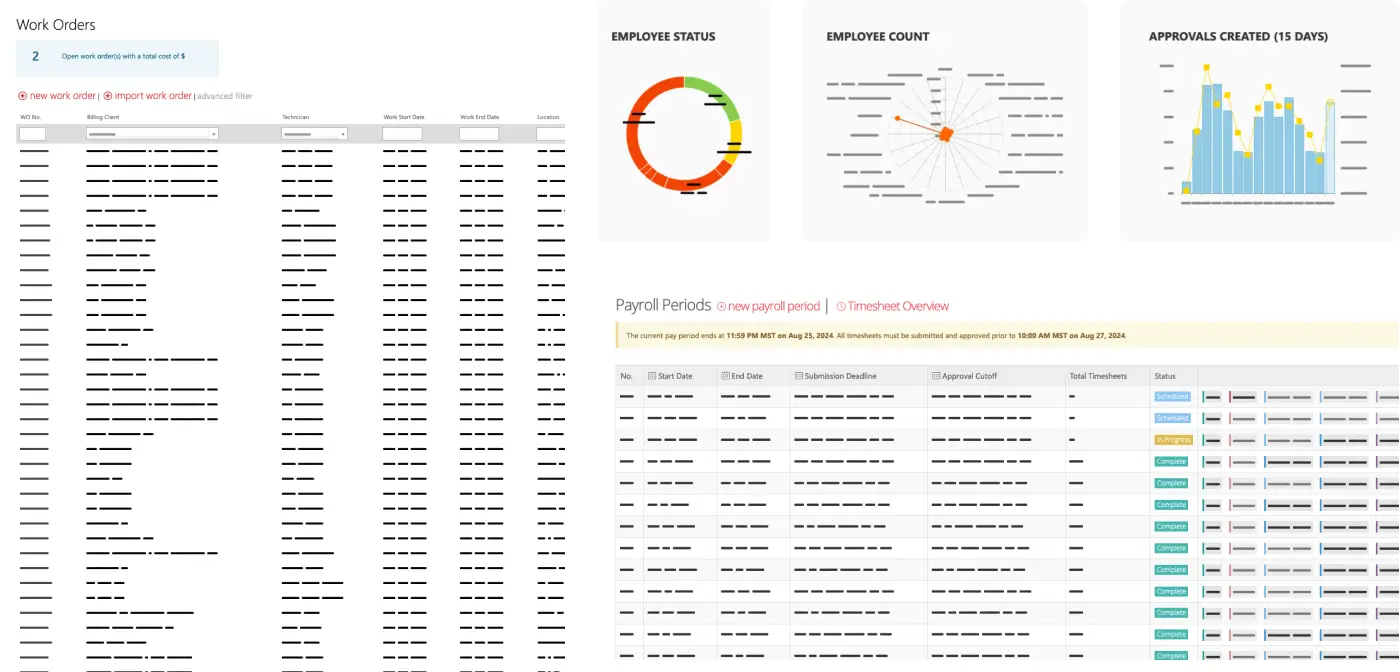

The Results

Increase in data accuracy, decrease in data entry and duplication errors, and reduction of unpaid invoices as a result of more precise and timely reporting

Decrease in time spent completing reporting and invoicing clients resulting in faster collection on account receivable

Instant access to paperwork and ability to monitor work orders in real-time resulting in complete transparency into field operations

Enhanced tracking of daily, weekly, and monthly revenue reporting and real-time productivity trends

Enhanced labor usage and project profitability tracking with integration into payroll and timesheet systems

Decrease in client support response time to project and billing inquiries with instant access to real-time data

Key Features

Creation of Unique Profiles
Ability to create profiles for technicians to upload their tickets and credentials to ensure certifications are kept up-to-date.

Creation of Digital Work Orders
Ability to create work orders with automatic calculations, discipline-specific report builder presets and automatic distribution to technicians.

Offline Data Synchronization
Ability to synchronize reporting data offline in the field remotely in real-time to a centralized platform.

Digital Time Sheet Tracking
Ability for technicians to digitally input time tracking while managers can approve hours directly integrated with payroll.

Upload External Data
Ability for technicians to upload notes, photos, recommendations, and other external assets tied directly to specific reports within the system.

Creation of Digital Invoices
Ability to create invoices integrated directly into financial platforms and accounting software like Quickbooks and Microsoft Dynamics that can then be sent directly to clients once a job is completed.

Track Equipment
Ability for managers to view calibration and maintenance schedules for all equipment in the field in real-time.

View Data Dashboards
Ability for administration users to monitor and track operational metrics and financial statistics in a visual data dashboard.

Technology Stack
Our talented and skilled development team at Punchcard leveraged the power of Microsoft .NET to design a robust application featuring both online and offline capabilities.
We also integrated Microsoft Dynamics NAV, an industry-recognized enterprise resource planning (ERP) tool, to efficiently manage and present data on human resources, operations, and sales.
The robust internal portal would integrate inputs and information from several different departments within Buffalo Inspection Services and output the data into a centralized database and financial dashboard.


“We had never built custom software before and had no idea what we were getting ourselves into. We had an initial idea but lacked resources to bring our vision to reality. Punchcard brought experience to the table and took the time to deeply understand our vision.”
Mark Friesen
Past Chief Financial Officer at Buffalo

About Buffalo Inspection Services
Founded in 1979, Buffalo Inspection Services is Canada’s largest non-union provider of Non-Destructive Testing (NDT) services for the mining, energy, industrial construction, and oil & gas industries.
For over 45 years, Buffalo has provided a full range of NDT services using the latest cutting-edge technology to inspect and test a variety of pipeline, midstream, and down-stream entities operating across Western Canada.

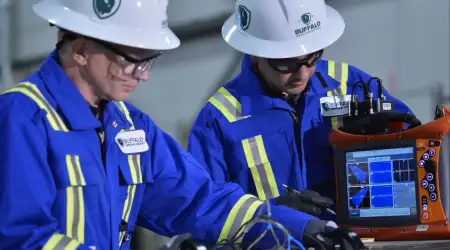
Non-Destructive Testing (NDT) is a critical safety inspection process that ensures the integrity of materials, components, and structures without causing damage.
Buffalo utilizes several innovative NDT techniques including ultrasonic testing (UT), magnetic particle testing (MT), liquid penetrant testing (PT), and radiographic testing (RT) to identify defects and irregularities in pipelines that could compromise worker safety and industry performance.
From preventing leaks and environmental hazards to monitoring equipment corrosion, Buffalo is critical in the early detection of defects—minimizing exorbitant repair costs, enhancing operational efficiency, and preventing catastrophic failure.
With a fleet of 60 crews and over 115 mobile units spread across 28 locations throughout Western Canada, Buffalo Inspection Services is the most trusted NDT partner in the oil & gas industry.


Conclusion
Buffalo Inspection Services’ journey with Punchcard Systems exemplifies how digital transformation can profoundly impact operational efficiency, data accuracy, and client satisfaction.
The continuous support and innovative solutions provided by Punchcard ensured that Buffalo could maintain its competitive edge in the oil and gas industry, demonstrating the transformative power of well-executed digital initiatives.

“Punchcard gave us the sense of persistence and confidence we needed to continue to persevere through this journey of scaling and transforming our business.”
Mark Friesen
Past Chief Financial Officer at Buffalo
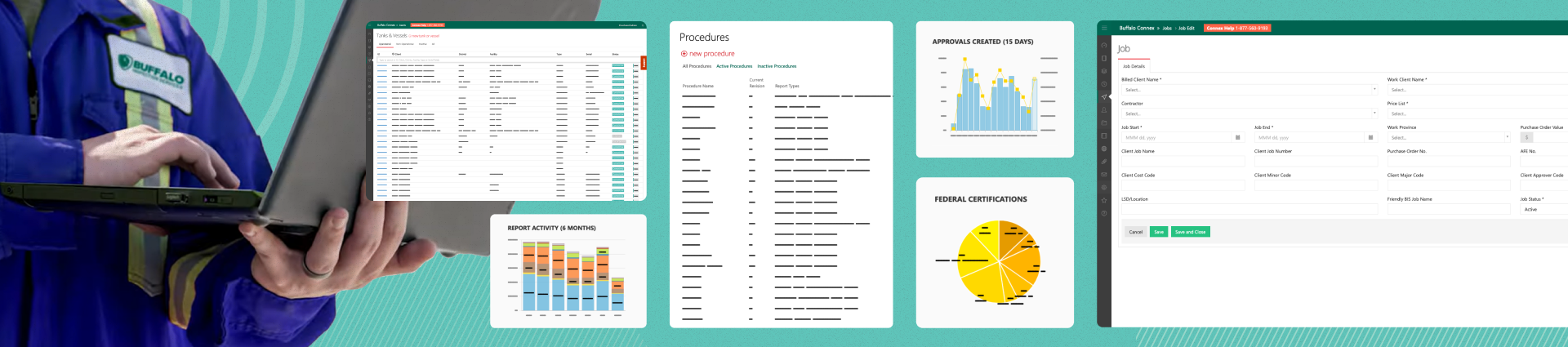